Impregnation Sealants
Impregnation sealants improve the integrity of components by sealing micro-porosities and eliminating potential leak paths enhance durable and surface finishing.
" With an unmatched portfolio of LOCTITE® products and our fully automated vacuum impregnation methods, we can ensure that customers no longer face the negative effects of porosities, including cost of scrapping, loss of production, dissatisfied customers or even lost business. Our state-of-the-art impregnation process technology gives you a permanent and reliable sealing solution to the problems of porosities and leakages. "
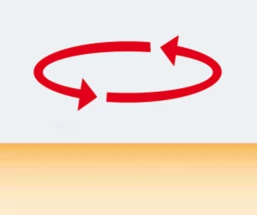
Step 1: Vacuum
Vacuum impregnation equipment, utilizing both dry and wet vacuum methods, prepares impregnation resin. Dry vacuum eliminates liquid interference, aiding effective degassing of pores. In the wet vacuum method, impregnation resin penetrates parts at atmospheric pressure, enabling swift processing. The resin then fills porosities, shrinkage cavities, capillary pores, and cracks, fortifying resistance to external influences.
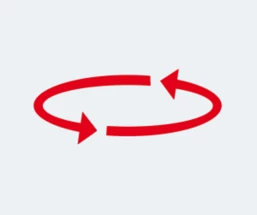
Step 2: Centrifuge
Excess sealant is removed from part surfaces through a drip-off and spin process; the most effective method for removing excess sealant with no risk of damage to the parts, while requiring very little time.
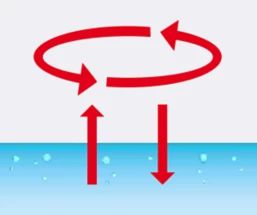
Step 3: Wash
Parts are washed, using the oscillator for agitation, and the centrifuge prepares for the rinsing step. Compressed air agitation in the water also may be used.
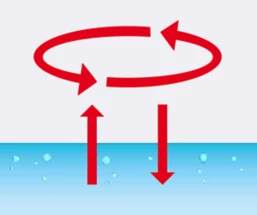
Step 4: Rinse
Parts are rinsed and the centrifuge prepares for the curing step. When exposed to the activator rinse, sealant at the pore entrances will cure quickly, creating a “plug” that prevents remaining liquid sealant from escaping while it continues to cure slowly by the anaerobic system.
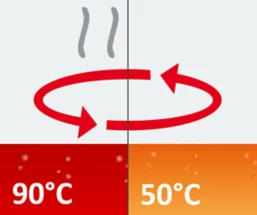
Step 5: Cure
Parts are soaked within a final rinse tank of water at 90°C (metal impregnation) or 50°C (electronic impregnation), removing the activator solution, and quickly drying and curing the part.
Vacuum impregnation methods ensure metal and electronics parts of vehicles are fully sealed against fluids, gases and other external influences and ready for just-in-time assembly. After impregnation, all parts are clean, free of corrosion or oxidation, and are ready for use without post-treatment. LOCTITE® vacuum impregnation solutions provide resins that cure to an impermeable thermoset polymer. This makes it possible to permanently seal pores or leakpaths to enable quality lightweight, thin-walled die-casted parts or electronic components.
Enquiry to process
The following chart will illustrate the general process of our screw patching service.
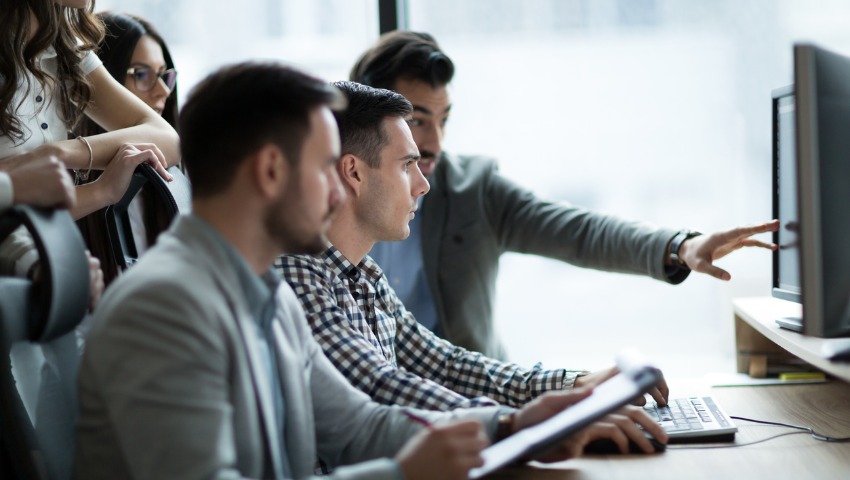
1. Initial Assessment
Begin with a detailed discussion with the customer to assess their impregnation sealant requirements. Understand the specific components, materials, and environmental conditions involved.
2. Technical Recommendation
Based on the assessment, provide a technical proposal outlining the recommended impregnation sealant. Consider factors such as material compatibility, application method, and expected outcomes.
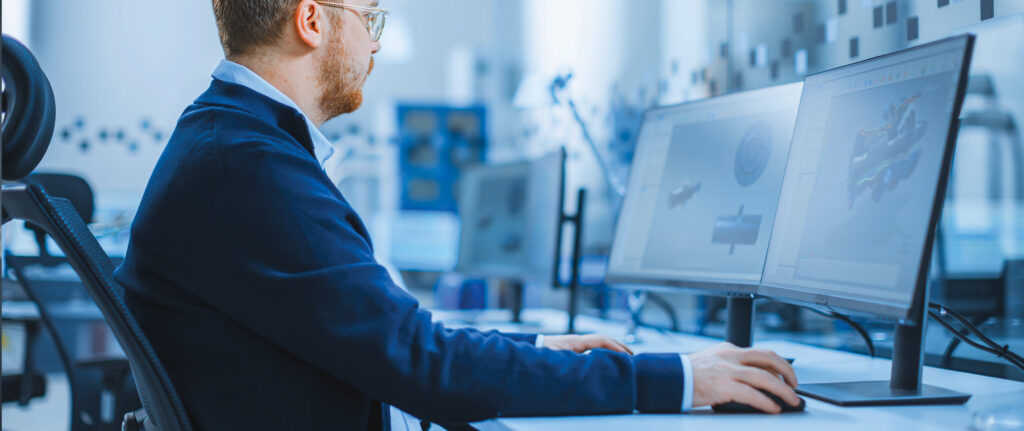
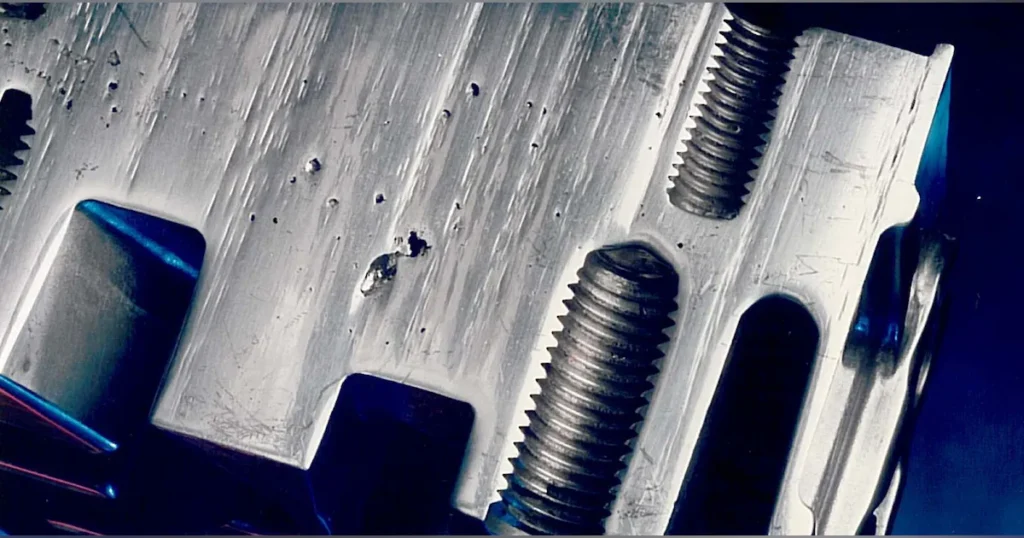
3. Prototype Application
Conduct a trial application of the impregnation sealant on sample components. Share the results with the customer, seeking feedback and making adjustments as necessary.
4. Tailoring Solutions
Customize the impregnation process based on customer feedback. Plan for the full-scale application, considering production volume and resource requirements.
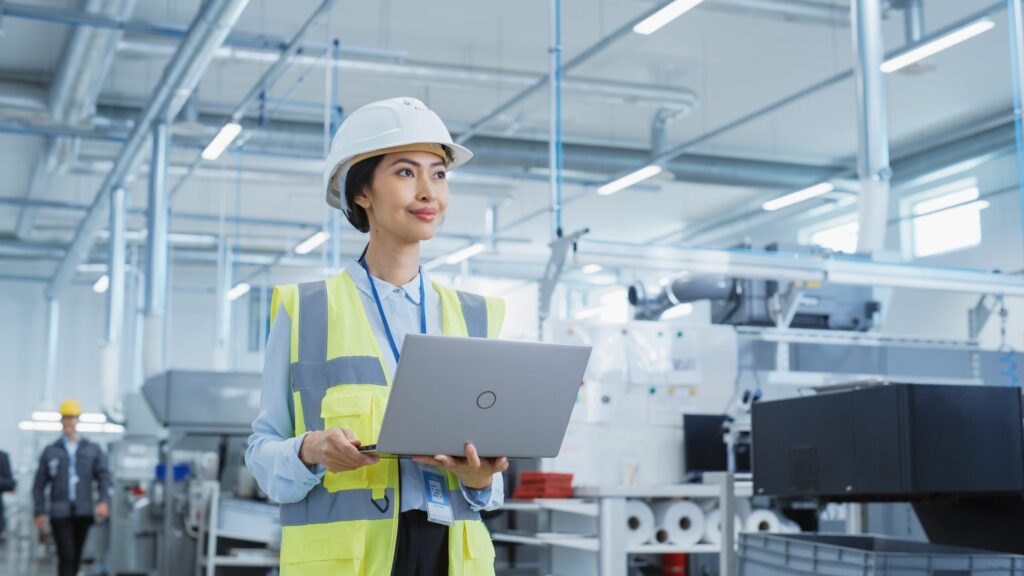
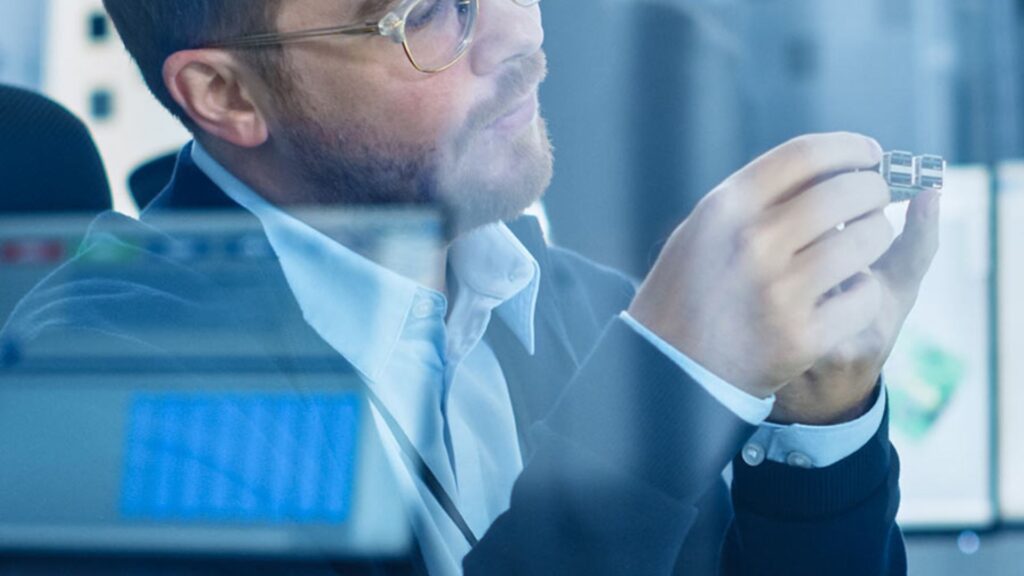
5. Rigorous Testing
Ensure the impregnation sealant meets quality standards through rigorous testing. Proceed with the application process, applying the sealant to the specified components.
6. Final Inspection and Delivery
Conduct a final inspection to verify the effectiveness of the impregnation sealant. Once confirmed, deliver the treated components to the customer, adhering to agreed-upon timelines.
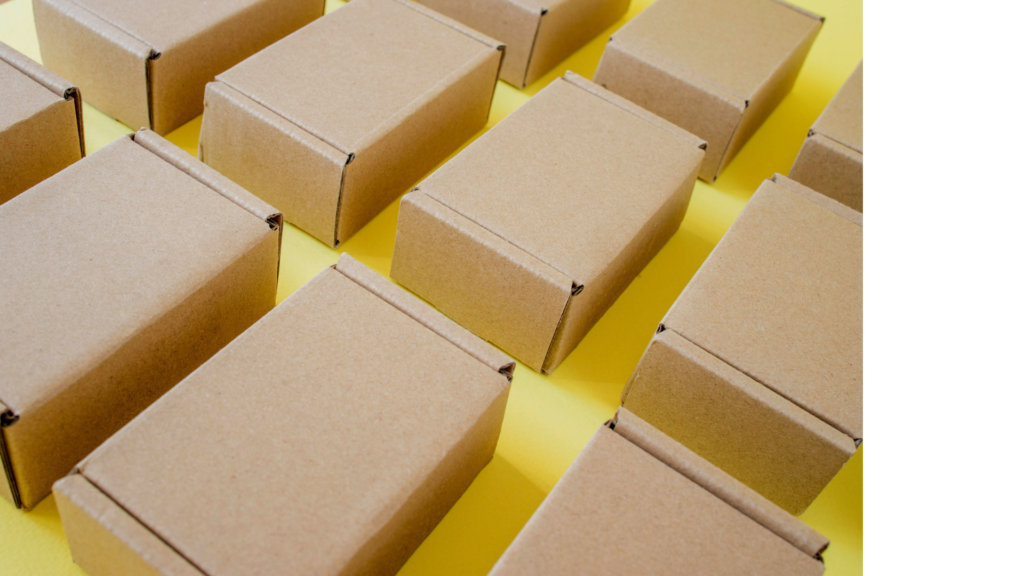
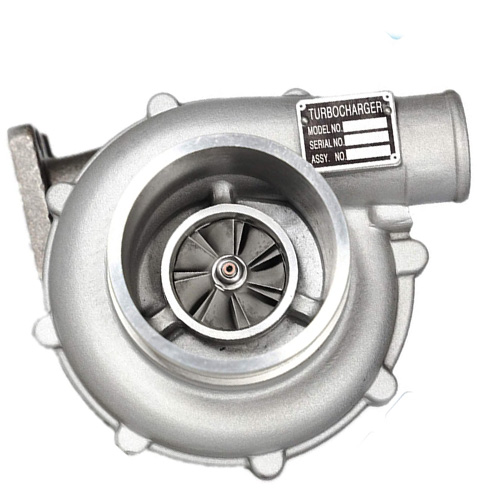